Efficiency in maintaining cold chambers, refrigerators and refrigerators is a constant challenge for the retail and distribution sector. With technological advancement, innovative solutions such as Above-NetBridgemeter® are transforming the way companies address the maintenance of these critical equipment.
The challenges
Monitoring of cold chambers in the food industry is not just a matter of a standard requirement; It involves a complexity of factors, including temperature homogeneity, moisture control, compressor status and components that ensure the structural integrity of the storage environment. The lack of proper monitoring in refrigerators and refrigerators poses significant risks to food safety, product quality and the reputation of the establishment, including:
- Food Safety: Inadequate temperature in refrigerators and refrigerators can compromise food safety, increasing the risk of bacterial contamination and product deterioration. This can lead to customer food poisoning, resulting in serious consequences for their health and well-being.
- Product Quality: Exposure to inadequate temperatures can affect the quality and freshness of food, resulting in financial losses for the supermarket. In addition, perishable products such as meat, dairy and fruits can lose their texture, taste and nutritional value when stored under inadequate conditions.
- Food waste: Lack of temperature and humidity monitoring can lead to food waste as products can spoil faster or be discarded due to worries about food safety. This not only represents an economic loss for the establishment, but it also contributes to the overall problem of food waste.
- Failure to comply with regulations: Establishments are subject to rigorous food safety regulations, which include specific requirements for the storage of refrigerated foods and records of periodic readings. Lack of proper monitoring of temperature and humidity may result in non -compliance with these regulations, subjecting the establishment to fines, penalties and even temporary closure.
- Damage to reputation: Food safety -related incidents such as dietary poisoning or low quality products can cause significant damage to the reputation of the supermarket. Loss customer confidence can lead to a reduction in sales, and negatively impact customer loyalty and long -term brand image.
Traditionally, this monitoring has been performed through manual inspections and eventually basic sensors, which not only consume time, but are also susceptible to human and technical failures. In addition, the lack of real -time information with predictive analysis means that many problems are only identified after damage occur, resulting in financial losses and, more seriously, risks to people's health, causing potential regulatory fines and legal costs .
Bridgemeter®: efficiency and forecast in the maintenance of cold chambers
Bridgemeter® implements an intelligent solution for IoT -based operational and maintenance management that transforms the operation of cold chambers, refrigerators and refrigerators. Through continuous monitoring and predictive analysis, the system allows early detection of potential failures, optimizing the maintenance process by intelligent notifications for the field team, accelerating care and avoiding unexpected interruptions.
With Bridgemeter®, companies considerably decrease the dependence on manual inspections, directing maintenance efforts efficiently. This not only reduces operating costs, but also extends the life of equipment and enhances the reliability of refrigerated storage. The ability to predict problems before it minimizes the risk of product loss and ensures a consistent customer experience.
Incorporating ROI into the equation
Bridgemeter® implementation offers a strong return on investment (ROI), with significant economies in maintenance and reduction of product losses. With an estimated (ROI) between 6 to 12 months, the solution not only pays rapidly, but also contributes to a more sustainable and efficient operation. Central predictive analysis of the system reduces the need for unnecessary inspection rounds and prevents unexpected breaks, emphasizing its position as a strategic investment for any operation that depends on cold storage. In addition, Brigmeter® is a multisectoral platform that allows the expansion of future monitoring to other sectors without an additional cost of hiring an additional system.
The adoption of Bridgemeter® signals a movement towards smarter and more efficient cooling assets and establishes a new standard for maintaining cold chambers.
Conclusion
Above-Net Bridgemeter® offers a revolutionary solution to maintenance challenges faced by retailers and distributors. By focusing on predictive analysis and optimization of the maintenance process, not only enhances operational efficiency by eliminating unnecessary inspection rounds, but also provides significant economies when avoiding unexpected equipment breaks, food deterioration, regulatory fines and legal costs. In addition, and most importantly, it offers an enhanced experience to the customer. In a competitive market, the ability to minimize unexpected interruptions and costs through predictive maintenance is a valuable strategic differential.
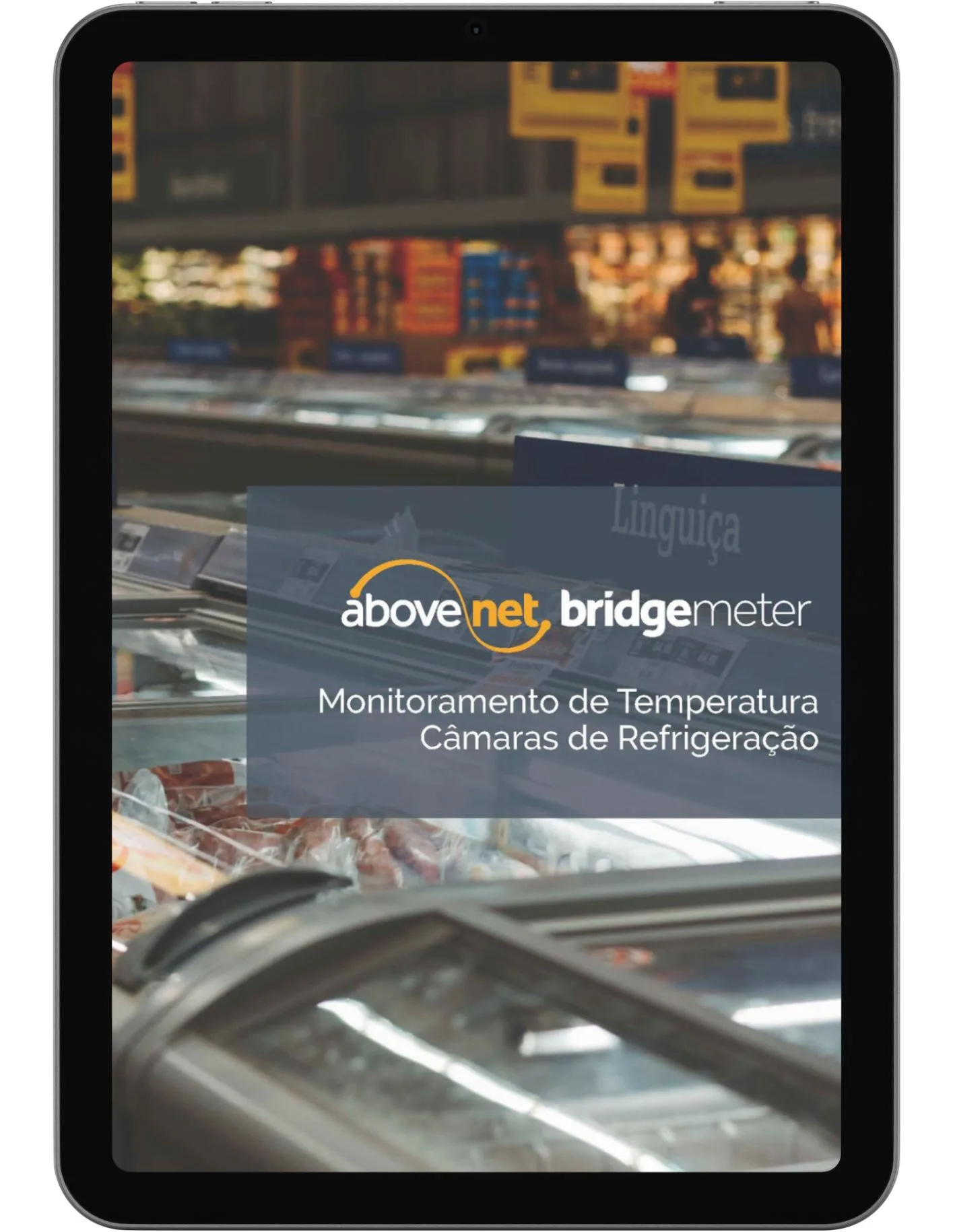
Catalog
Want to know more how to improve the efficiency in maintaining cold chambers, refrigerators and refrigerators through predictive monitoring?
Then download our temperature monitoring catalog of cooling chambers and ensure operational efficiency and the quality of your product with intelligent industrial IoT solution.
Also read:
Above-Net advances with more intelligent IIOT installations for sanitation
The importance of hospital infrastructure: case study on preventable losses