The Internet of Industrial Things (IIOT) has emerged as a transformative force in the sectors with critical applications, revolutionizing the way companies operate, monitor and optimize their production processes. The implementation of IIOT in processes is no longer an option, but an urgent need, driven by the constant search for operational efficiency, cost reduction and increased competitiveness in the global market.
Digital Transformation in Industry
IOTA's ability to connect machines, devices and systems allows real -time data collection and analysis by offering valuable insights that can lead to significant improvements in efficiency, productivity and sustainability. Through the automation and intelligence provided by IIOT, industries can achieve a level of accuracy and control over their production processes that was unimaginable just a decade ago.
In addition, the incorporation of IIOT into industrial processes enables continuous and predictive monitoring of equipment. This makes it possible to detect in advance possible failures or inefficiencies, preventing them from becoming more serious problems. This approach not only decreases the time of inactivity and the costs related to corrective maintenance, but also extends the life of equipment and ensures employee safety.
It is noteworthy that IIOT is just a step towards digital transformation and that its applications are endless with gains often not yet measured in various segments for this multiplicity. Regardless, IIOT transforms and revolutionizes the sector where it goes by offering unprecedented opportunities for efficiency and continuous cost reduction as we will see in the examples below.
Types of processes that can be optimized with IIOT in manufacturing
1) Process control
It involves the surveillance and management of any critical variables of processes such as voltage, current, temperature, pressure, flow, and many others to ensure effective and secure operation of industrial machinery and systems. Through intelligent IIiot monitoring, connected sensors capture data in real time of these variables, allowing precise and continuous analysis of process performance. With intelligent algorithms and predictive analysis, the system can identify patterns, anomalies and trends, offering valuable insights and alerts for failure optimization and prevention. In addition, integration with automated edge equipment and control systems enables automatic adjustments and precise remote interventions, ensuring more efficient, reliable and safe operation.
2) ENGINEERING AND MAINTENANCE OF EQUIPMENT
It comprises the complete management of the life of industrial machinery and equipment, from its installation to inspection, maintenance and repair, aiming to ensure efficient functioning and prevent failures. Through Intelligent IOT Monitoring, it is possible to collect real -time data on the performance and condition of equipment, allowing a proactive analysis of maintenance needs. Advanced data analysis algorithms can identify wear patterns, suggest preventive maintenance, and predict possible failures before they occur, reducing unprourse inactivity time and increasing operational reliability. Thus, engineering and maintenance of equipment becomes more effective and efficient, ensuring continuous and secure operation of industrial facilities.
3) Emissions and pollutant management
It encompasses a series of procedures designed to control and minimize gas emissions, liquid effluents and other harmful pollutants to the environment. This involves monitoring and managing a variety of critical variables, such as turgidity, pH, chlorine level, CO2, membrane inlaid, among others. Using intelligent IIOT Monitoring Systems, it is possible to collect real -time data from these variables, allowing a detailed analysis of the performance of pollution control processes. With advanced data analysis algorithms, it is possible to identify emission patterns, evaluate the effectiveness of effluent filtering and treatment systems, and optimize the performance of emission reduction technologies. In integrating cutting-edge technologies with environmental management practices, emissions and pollutant management becomes more effective and sustainable, contributing to the preservation of the environment and regulatory compliance.
4) Infrastructure and climate control management
It covers a number of procedures designed to control and optimize the infrastructure of industrial buildings and facilities to ensure a safe, comfortable and efficient environment. This includes monitoring and control of variables such as humidity, temperature, opening of loading/discharge doors to ensure the efficiency of cooling and heating systems. In addition, cooling towers monitoring is essential, with important variables such as water temperature, voltage and current being closely monitored. Unexpected stops of these infrastructure equipment can result in significant interruptions in operations and even damage to heat -sensitive products and equipment. Therefore, continuous monitoring of these variables is crucial to identifying and solving problems before negative impacts. By using smart IOT Monitoring Systems, companies can get real -time insights on infrastructure performance and proactively implement corrective actions, ensuring continuous and efficient operation.
5) Integration and interoperability of assets and supervisory
This field covers the implementation of an architecture optimized for the monitoring of industrial processes, taking advantage of technologies such as programmable logic controllers (PLCs), supervision systems and data acquisition (SCADA) and robotics. Improving interoperability is critical to ensuring effective communication between these systems, allowing data collection and analysis and eventual need for remote intervention in real time in an integrated manner. Remote telemetry and monitoring systems play a crucial role in this process, offering a unified architecture to access and manage remote assets efficiently, allowing the integration between PLCs and SCADA systems in a transparent and broader way. This improved interoperability not only increases operational efficiency, but also offers greater visibility, flexibility and control over industrial processes, resulting in more informed and proactive decision making.
6) Energy Management
This area covers a series of processes aimed at optimizing energy use in industrial environments. This includes detailed analysis of energy consumption, monitoring important variables such as demand, voltage, electric current, and subsystems such as battery backup and generators. In addition, the implementation of efficient energy systems is essential to reduce waste and maximize operational efficiency. The integration of renewable energy sources, such as solar or wind, also plays an important role in the search for a more sustainable and eco-friendly operation. This integrated approach not only helps reduce operating costs, but also contributes to the reduction of carbon footprint and long -term environmental sustainability.
7) Standardization and regulatory compliance
Processes to ensure that industrial operations comply with national and international rules and regulations, including safety, environmental and quality standards.
8) Process integration for automation
It involves the development and maintenance of integrated systems that facilitate efficient communication and coordination between various processes and departments in industrial environments. A significant advantage of this integration is the automation of certain processes, such as issuing service or purchase orders request, during failure unfolding or detecting anomalies confirmed by the field maintenance team. The use of an integrated intelligent IOT platform, which allows a quick and accurate response to operational needs, increases efficiency, reduces inactivity time and makes the process 100% digital.
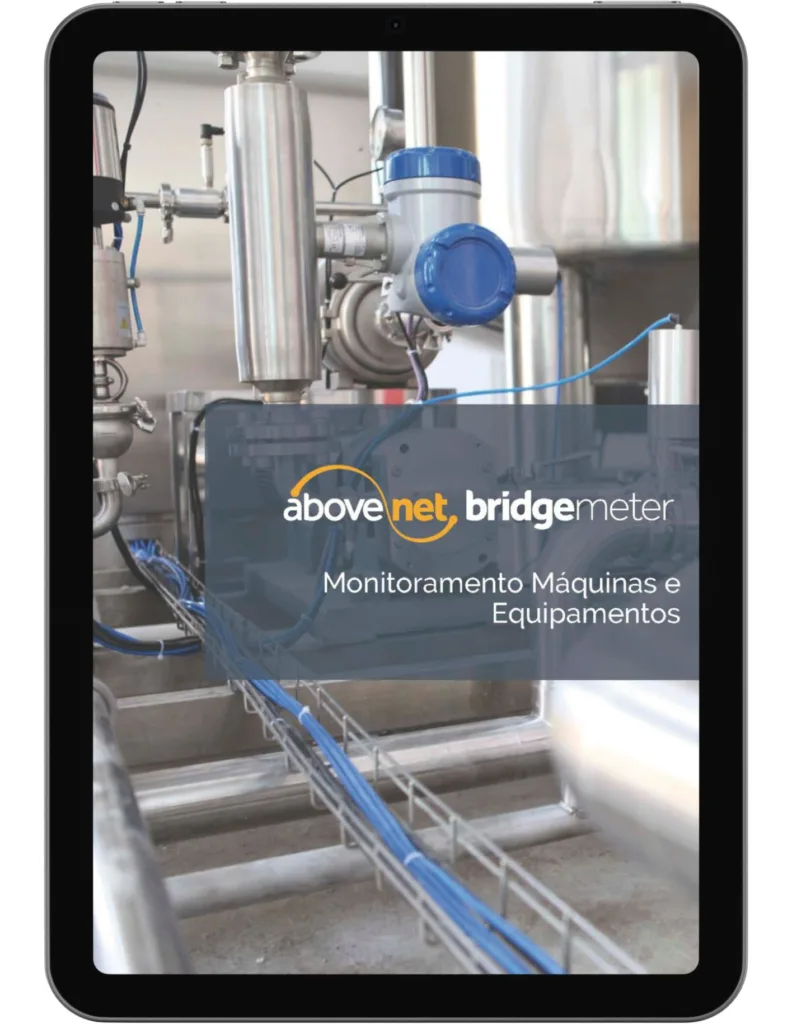
Application
Avoid unplanned interruptions with monitoring machines and equipment
The machine and equipment monitoring catalog shows how Bridgemeter offer intelligent predictive monitoring and remote control of machines and equipment, improving efficiency and productivity in its industrial plant, while reducing risks and maintenance costs.
Also read:
Energy efficiency in industry: the growing importance of intelligent monitoring