Dans l’environnement industriel, l’efficacité et l’agilité sont cruciales. Imaginez l'équipe de production ajoutant de nouveaux équipements au système de surveillance actuel. Avec les systèmes SCADA traditionnels, cette tâche peut se transformer en un véritable cauchemar, prenant jusqu'à six mois entre la demande, le budget, la mise en œuvre et la configuration des tableaux synoptiques nécessitant des conseils spécialisés.
Durant cette période, l’entreprise fait face à une série de défis qui pourraient compromettre son fonctionnement.
Complexité et temps d'installation
Ajouter un point de mesure à un système de surveillance traditionnel n'est pas une tâche facile et implique plusieurs étapes, de la connectivité des équipements à distance à la configuration des TAG et des synoptiques, en passant par les alarmes et la mise à jour des tableaux de bord existants.
En moyenne, une entreprise peut attendre 3 à 6 mois pour terminer le processus, car cela dépend la plupart du temps de licences, de main d'œuvre spécialisée en interne et en tiers, ainsi que, bien sûr, de coûts supplémentaires.
Le processus de production fonctionne donc sous des risques, soumis à une efficacité opérationnelle réduite et à des coûts élevés. Pendant cette période, la surveillance n’est pas fiable, gaspillant des ressources précieuses et augmentant le risque de défaillances opérationnelles.
Conséquences pour l'entreprise
Le retard dans la configuration des nouveaux équipements et fonctionnalités génère une cascade de problèmes pour l’entreprise. L'exploitation peut connaître des événements imprévus qui, s'ils ne sont pas surveillés, réduisent la capacité de livraison conformément aux engagements pris, affectant la satisfaction des clients et, à terme, les revenus.
L'entreprise est confrontée à des coûts supplémentaires pour les conseils et les réparations, tandis que le manque de surveillance adéquate augmente le risque de pannes et de temps d'arrêt imprévus. La compétitivité de l'entreprise est compromise, ce qui rend difficile la réponse rapide aux changements du marché et aux demandes des clients.
L'impact sur l'ingénierie de production
Pour l’ingénieur de production, la situation est tout aussi difficile. La nécessité de mettre en place un nouveau point de contrôle augmente avec le risque et la responsabilité des retards. Le recours à des consultants externes réduit votre autonomie, vous rendant moins en mesure de répondre rapidement aux problèmes opérationnels. Si des pannes ou des arrêts surviennent pendant le délai de configuration, l'ingénieur devra gérer les crises, coordonnant les réparations sous une pression intense. De plus, il perd l'orientation principale de son travail sur l'amélioration et l'innovation de la production, limitant ainsi son potentiel de contribution à l'efficacité et à la croissance de l'entreprise.
Le danger des défauts non détectés
Imaginez le scénario dans lequel une machine critique en fonctionnement attend la fin de la configuration du système de supervision de la ligne de production et fonctionne sans système capable d'indiquer les problèmes à distance.
Si ces défauts ne sont pas détectés à temps, la machine s’arrête, affectant la capacité de production de l’ensemble du processus. Les conséquences sont graves : l’entreprise perd du volume de production, fait face à des coûts de réparation élevés et ses revenus s’effondrent. La réputation de l'entreprise en souffre et les clients mécontents commencent à remettre en question la fiabilité des livraisons.
La solution
Il n'y a qu'une seule façon de résoudre le problème. Vous avez besoin d’une solution avec un système qui comprend les caractéristiques suivantes :
- Configuration rapide et intuitive par glisser-déposer ;
- Connexion à tout type de machine, capteur ou système ;
- Système de notification configurable proactif ;
- Si nécessaire, intégrable aux systèmes SCADA.
Besoin d'une recommandation ?
Bridgemeter est la plateforme IoT industrielle intelligente qui résout tous ces problèmes rencontrés sur le marché.
Au lieu d'attendre des mois et de faire appel à des conseils extérieurs, l'ingénieur de production peut utiliser l'éditeur intuitif glisser-déposer de Bridgemeter pour créer un tableau synoptique détaillé en quelques minutes. Il reçoit une alarme dans son application lui indiquant des anomalies, des variations et des calculs hors plan. Grâce à l'alerte prédictive de Bridgemeter , l'équipe de maintenance est en mesure d'identifier rapidement les causes des problèmes, de consulter la documentation et d'enregistrer la maintenance, garantissant ainsi la poursuite de la production sans interruption.
Avantages pour l'entreprise et l'ingénieur
Avec Bridgemeter , l'entreprise évite les délais et les coûts associés à la lente intégration des nouveaux équipements. La production reste efficace et le risque de panne est considérablement réduit. L'entreprise peut répondre rapidement aux demandes du marché, maintenir sa compétitivité et garantir la satisfaction de ses clients. Pour l’ingénieur de production, plus de sécurité et de confiance. Il gagne en autonomie pour configurer et surveiller rapidement les équipements, en évitant les crises et en se concentrant sur les domaines d'amélioration et d'innovation. Bridgemeter transforme le mode de fonctionnement de l'entreprise, en offrant agilité, efficacité et tranquillité d'esprit.
- Installation rapide et facile
- Éditeur intuitif de glisser-déposer
- Indépendance opérationnelle
- Prévention des pannes et des arrêts
Découvrez comment nos solutions peuvent transformer votre activité :
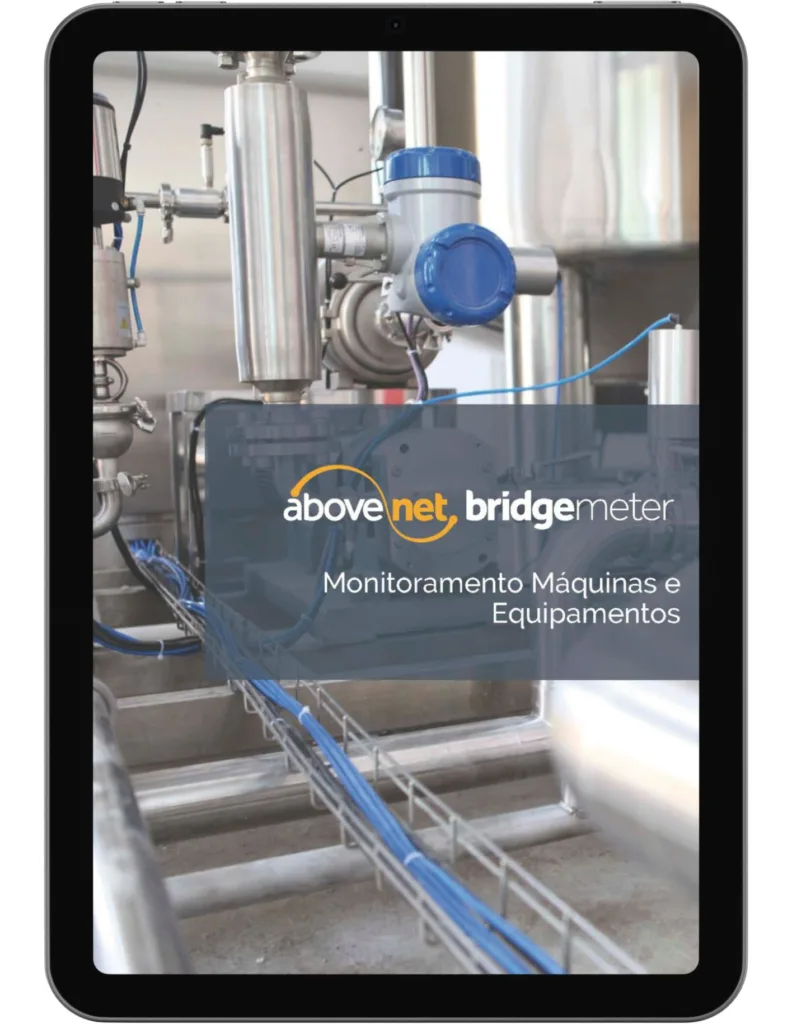
Application
Évitez les pannes imprévues grâce à la surveillance des machines et des équipements
Le catalogue Surveillance des machines et des équipements montre comment Bridgemeter fournit une surveillance prédictive intelligente et un contrôle à distance des machines et des équipements, améliorant ainsi l'efficacité et la productivité de votre installation industrielle tout en réduisant les risques et les coûts de maintenance.
A lire aussi :
Quels types de processus bénéficient de l’IoT industriel dans le secteur manufacturier ?