En el entorno industrial, la eficiencia y la agilidad son cruciales. Imagine al equipo de producción agregando nuevos equipos al sistema de monitoreo actual. Con los sistemas SCADA tradicionales, esta tarea puede convertirse en una auténtica pesadilla, tardando hasta seis meses entre la solicitud, el presupuesto, la implementación y la configuración de cuadros sinópticos que requieren consultoría especializada.
Durante este período, la empresa enfrenta una serie de desafíos que podrían comprometer su operación.
Complejidad y tiempo de configuración
Agregar un punto de medición a un sistema de monitoreo tradicional no es una tarea fácil e involucra varios pasos, desde la conectividad remota del equipo hasta la configuración de TAG y configuración sinóptica, alarmas y actualización de tableros existentes.
En promedio, una empresa puede esperar de 3 a 6 meses para completar el proceso, ya que la mayoría de las veces depende de licencias, mano de obra especializada propia y de terceros, además de, por supuesto, costos adicionales.
Por lo tanto, el proceso de producción opera bajo riesgos, sujeto a una eficiencia operativa reducida y costos elevados. Durante este período, el monitoreo no es confiable, lo que desperdicia recursos valiosos y aumenta el riesgo de fallas operativas.
Consecuencias para la empresa
El retraso en la configuración de nuevos equipos y funcionalidades genera una cascada de problemas para la empresa. La operación puede experimentar imprevistos, que de no ser monitoreados, reducen la capacidad de entrega de acuerdo con los compromisos adquiridos, afectando la satisfacción del cliente y, en definitiva, los ingresos.
La empresa enfrenta costos adicionales de consultoría y reparaciones, mientras que la falta de un monitoreo adecuado aumenta el riesgo de fallas y tiempos de inactividad inesperados. La competitividad de la empresa está comprometida, lo que dificulta responder rápidamente a los cambios del mercado y las demandas de los clientes.
El impacto en la ingeniería de producción
Para el ingeniero de producción la situación es igualmente complicada. La necesidad de establecer un nuevo punto de seguimiento aumenta con el riesgo y la responsabilidad por los retrasos. La dependencia de consultores externos reduce su autonomía, lo que le hace menos capaz de responder con prontitud a los problemas operativos. Si se producen fallos o paradas durante el retraso de la configuración, el ingeniero tendrá que gestionar las crisis, coordinando las reparaciones bajo una intensa presión. Además, pierde el foco principal de su trabajo en mejorar e innovar la producción, limitando su potencial para contribuir a la eficiencia y el crecimiento de la empresa.
El peligro de fallos no detectados
Imagine el escenario en el que una máquina crítica en funcionamiento espera que se complete la configuración del sistema de supervisión de la línea de producción y opera sin un sistema que pueda indicar problemas de forma remota.
Si estas fallas no se detectan a tiempo, la máquina se detiene, afectando la capacidad de producción de todo el proceso. Las consecuencias son graves: la empresa pierde volumen de producción, enfrenta altos costos de reparación y sus ingresos se desploman. La reputación de la empresa se resiente y los clientes insatisfechos empiezan a cuestionar la fiabilidad de las entregas.
La solución
Sólo hay una manera de resolver el problema. Necesita una solución con un sistema que incluya las siguientes características:
- Configuración rápida e intuitiva de arrastrar y soltar;
- Conexión a cualquier tipo de máquina, sensor o sistema;
- Sistema de notificación configurable proactivo;
- Si es necesario, integrable con sistemas SCADA.
¿Necesitas una recomendación?
Bridgemeter es la plataforma IoT industrial inteligente que soluciona todos estos problemas encontrados en el mercado.
En lugar de esperar meses y depender de consultoría externa, el ingeniero de producción puede utilizar el editor intuitivo de arrastrar y soltar de Bridgemeter para crear una tabla sinóptica detallada en cuestión de minutos. Recibe una alarma en su aplicación indicando anomalías, variaciones y cálculos fuera de lo previsto. Gracias a las alertas predictivas de Bridgemeter , el equipo de mantenimiento puede identificar rápidamente las causas de los problemas, consultar la documentación y registrar el mantenimiento, asegurando que la producción continúe sin interrupciones.
Beneficios para la Empresa y el Ingeniero
Con Bridgemeter , la empresa evita los retrasos y costos asociados con la lenta integración de nuevos equipos. La producción sigue siendo eficiente y el riesgo de fallos se reduce significativamente. La empresa puede responder rápidamente a las demandas del mercado, manteniendo su competitividad y garantizando la satisfacción del cliente. Para el ingeniero de producción, más seguridad y confianza. Gana autonomía para configurar y monitorear rápidamente los equipos, evitando crisis y enfocándose en áreas de mejora e innovación. Bridgemeter transforma la forma de operar de la empresa, aportando agilidad, eficiencia y tranquilidad.
- Configuración rápida y sencilla
- Editor intuitivo de arrastrar y soltar
- Independencia operativa
- Prevención de Averías y Paradas
Vea cómo nuestras soluciones pueden transformar su operación:
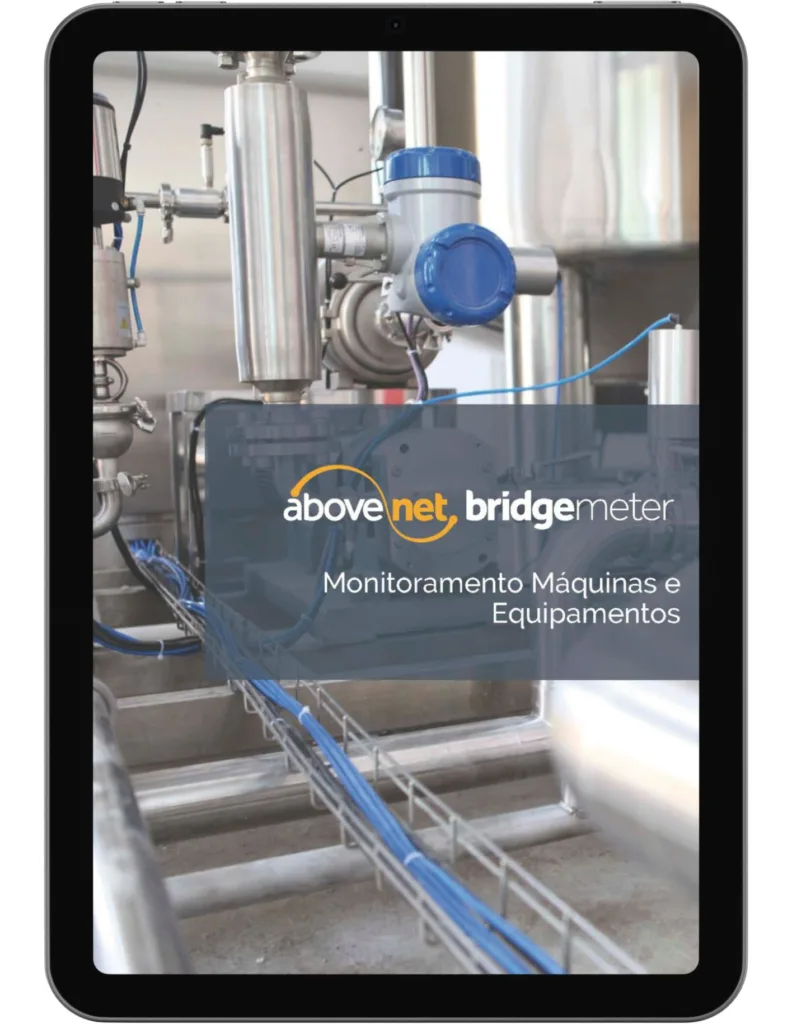
Solicitud
Evite interrupciones no planificadas con el monitoreo de máquinas y equipos
El catálogo de Monitoreo de Máquinas y Equipos muestra cómo Bridgemeter proporciona monitoreo predictivo inteligente y control remoto de máquinas y equipos, mejorando la eficiencia y la productividad en su planta industrial al tiempo que reduce los riesgos y los costos de mantenimiento.
Lea también:
Desafíos tecnológicos que enfrentan los fabricantes de máquinas en monitoreo y análisis predictivo
¿Qué tipos de procesos se benefician del IoT industrial en la fabricación?